What is Production Capability & How Do You Build It in Your Organisation?
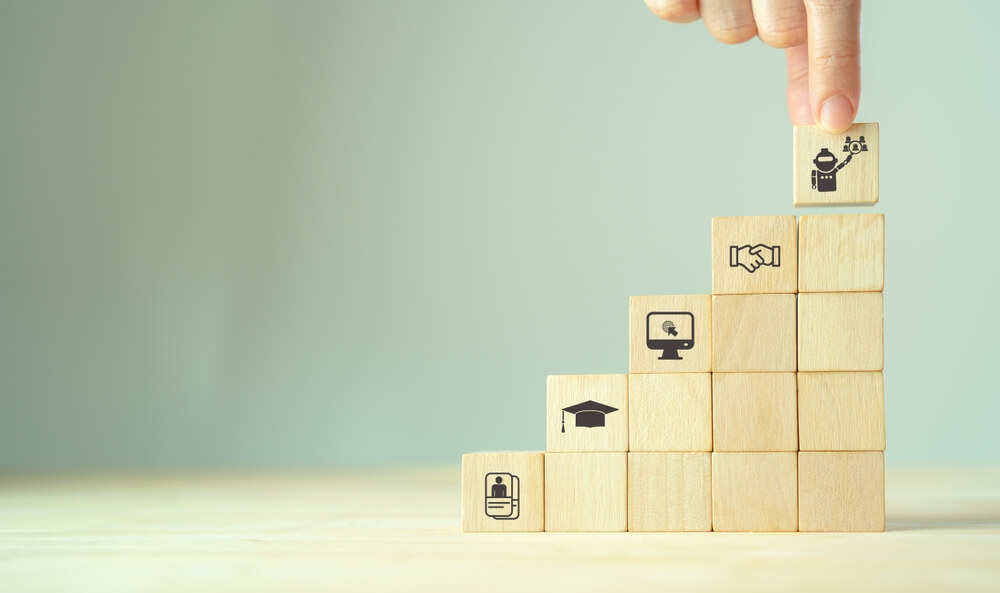
Discover how to define production capabilities, plus get a six-step guide for building production capability for sustainability and profitability
Production, of all business units, can’t afford to be inefficient or ineffective. That comes down to ways of work and how you codify high performance through production capability.
But defining and developing production capability isn’t always an easy task with so many moving parts. That’s why we’ve got you started in this guide, with a rundown on how to create production capabilities from scratch and a step-by-step process for building production capability in your workforce. Let’s dive in.
What is production capability?
Production capability refers to the collective skills, knowledge, behaviours, processes and tools required for an organisation to deliver its goals through its production function.
3 steps to define production capabilities
Given production can be centralised within one internal department or a combination of a few specialised functions and outsourced labour, defining clear-cut guardrails for performance is pretty important. It could be the difference between optimising a process or bottlenecks appearing left, right and centre.
Step 1: Define the landscape
All capability building starts with understanding the business landscape, position and future plans. The aim is to ensure true strategic alignment between production and business goals.
- Start by considering the organisation’s broader mission, purpose and values
- Outline the production department’s role in that mission
- Finish by defining production’s value as a function, now and into the future.
Step 2: Define the purpose
The next port of call is to ask what purpose production capability serves. Each capability defined should play a unique role, based on five factors.
- Company strategy: Will said capability help your organisation achieve its goals?
- Market need: Is there a demand for it in the market?
- Resources: Do you have capacity across people, budget and equipment to sustain it?
- Current capabilities: Are you cannibalising existing capabilities in your organisation?
- Risks: Would you risk harm to reputation or finances with this capability?
In layman’s terms: What is this capability meant to do?
Step 3: Define the outcome
Time to put a name to the face—ahem, capability. When you know what it does, you can describe a capability in a way that makes sense for your workforce. We say workforce, because if you intend to use production capabilities are a true organisational development tool, they need to be universally understandable.
Think:
- Increased delivery speed
- Production cost control and budgeting
- Managing and scheduling production runs.
Now, if naming every single production process seems a little daunting, you needn’t fear. We’ve got a fairly comprehensive library of production capabilities available for free here. You can copy, download and edit them as you need.
We just recommend that you change up any language necessary to make sense in the context of your organisation. (Although, if you like how we’ve worded it, you’re welcome to use as is!)
Strategies for building production capability
While the nuances of building production capability are distinct to production, the general process for developing that capability is pretty foundational. It looks like:
- Engage leadership for cultural buy-in
- Create co-owned accountability
- Establish capability gaps (at the individual level)
- Assess capability maturity (for the organisation)
- Create methods for building capability
- Review and track progress.
Engaging leadership
As with many functional leaders, production leaders are responsible for a lot of moving parts. They occupy an unparalleled space as the cultural and strategic lynchpin for the function.
Getting their buy-in is important on both of those fronts. You create champions for capability building within the workforce, and you also gain their insight to create truly timely interventions. You just need to speak their language.
Start with their pain points (as problems solved are always an easy win). Perhaps technology and machinery are moving faster than they can keep up? Do they lack the measures to assess process variations in real time? In terms of talent, do they have the right roles to match industry pace?
If you can position capability building as the solution to their real problems, you’re:
- Aligning everyone around KPIs and, therefore, business impacts
- Breaking crucial processes and tasks down by the skills, knowledge, behaviours and tools that drive them, showing a replicable path to success.
Co-ownership between HR and production
On the back of understanding their needs, you need to outline who is accountable for what during the capability building process. Don’t think of each business unit as an autonomous entity here. You’re all working towards that same goal.
For starters, HR should retain control of capability building through the lens of organisational development. Where co-ownership kicks in is with the specific needs of local production capability. Use their time efficiently at two major milestones:
- Gathering proactive insight into the talent they need now versus what is needed to support future plans
- Garnering cultural buy-in for the doing (see “Methods for building production capability” below) of capability building.
Without either set of information, HR is working on a lot of assumptions. And that makes it harder to embed new ways of work in the workforce, while simultaneously making it easier for the workforce to resist change.
Understanding production capability gaps
Here’s where we start to get really prescriptive to production as a function.
Assessing capability gaps generally requires a holistic view of performance. We can do that through three types of assessments.
- The self-assessment asks employees to evaluate their current level of competency for a set of job-related capabilities.
- Manager assessments get, you guessed it, managers to evaluate an employee. It’s usually best to do this against the same capabilities the employee self-assesses for more constructive performance discussions.
- Subject matter expert assessments are used for more specialist capability sets, so are not relevant for every employee.
You can’t undertake proper planning for L&D without this step. The point is to establish a baseline for development plans. If you embed that into your evaluation criteria, it gives everyone a clear understanding of performance needs.
Assessing production capability maturity
The high-level view of gaps is capability maturity. When that comes to production, this is a crucial step that’ll show you capacity in real time. This information allows you to justify resourcing and planning, FYI.
The criterion for assessing maturity is up to you, but it’s best to measure on some scale of business risk versus availability. However, the scale for maturity follows the same five stepping stones.
- Initial
- Managed
- Defined
- Qualitatively managed
- Optimised.
Each point represents the way capability work gets done. So, initial would mean it occurs but is largely unpredictable, while optimised refers to seeking continuous improvement through a fine-tuned process.
Data is commonly presented in a visual heatmap, where the most at-risk capabilities (and therefore those to be prioritised for development) appear in red. That way, prioritisation decisions are both incontrovertible and understandable for all stakeholders.
Methods to build production capability
The specific ins and outs of learning content will be up to you here. The point is that you contextualise our recommendations, because without demonstrating exactly how employees should apply new knowledge, you risk poor knowledge retention or even conflicting ways of work. All of which negates the whole point of this endeavour: Behavioural change.
And if you’re trying to change habits, mindsets and processes, then you need development methods to reflect the environment in which that change needs to occur. Time is usually of the essence for production, so you don’t want to take employees out of the workday unless absolutely necessary.
Look to:
- Coaching and mentoring. This can be as simple as peer mentoring during onboarding or a more formal effort that pairs a senior production employee with a junior worker. Of note: This is a great way to nurture the behavioural aspect of capability building.
- Knowledge management systems. They’re crucial for creating a source of truth for critical information. You’d still need subject matter experts to act as information owners, but the point is that you’re making key information easily accessible. A performance learning management system (PLMS) can help allocate capabilities and contextual learning opportunities to drive organisational improvement.
- On-demand learning content. Piggybacking off the knowledge system, this would have to be meticulously kept up to date, but it means that employees can access videos or step-by-step guides to DIY their knowledge gaps. And that’s key to ensuring they don’t look externally for answers to internal questions.
Tracking progress
Likely, you already account for process variation somewhere in your production processes. This isn’t a dissimilar concept. You’re looking for inefficient or defective areas of the capability building process to eliminate, or areas of value to amplify.
Reassessments can help you determine training efficacy on a couple of fronts. First, the relevance of training content, and second, the accuracy of training design.
Start with:
- Proactive needs analyses that re-scan the business environment. That way you can be sure that capability gaps are truly high risk and training methods are therefore going to have the greatest impact on employees and business.
- If you’re using a knowledge management system, consider its reporting functionality. Common L&D metrics like completion rates and assessment scores give a baseline of learner engagement and time to proficiency. Use surveys here to gather employee sentiment, the clearest idea of relevance and impact.
- Embed performance management into capability building, so reviews and development become parallel processes. You get the added benefit of continuous feedback loops, and you’re simultaneously ensuring managers are all teaching the same thing.
Key takeaways
While there’ll be a complex combination of market requirements for and internal nuances to your organisation’s production capabilities, it pays to spend the time outlining them as clearly as possible. Production capability will underpin the sustainability and profitability of your production function, giving you a replicable path for success in future.
Building that capability should be an involved process starting with:
- Engaging leadership for cultural buy-in and real-time talent needs
- Establishing co-ownership for the entire process between production leaders and HR
- Assessing capability gaps to understand individual performance needs
- Evaluating capability maturity to get a high-level view of production capability in your organisation
- Embed learning in the flow of work to create the most relevant training experiences
- Continuously review methodology in the name of improvement.